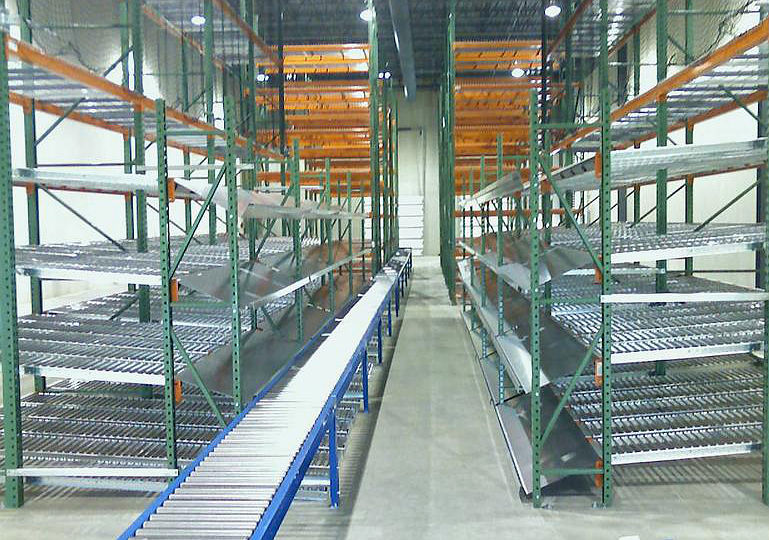
Pick module systems are engineered rack systems that employ rack components incorporated to several storage solutions. They are designed to efficiently move products through a distribution center to hurry up the process of order fulfillment. These are created to optimize the efficient flow of multiple orders specifically in business warehouses.
Usually, pick module systems enable the automatic transport of palletized loads through gravity. The loads are aimed at storage in the flow racks or they can be split into individual products to be prepared for the shipment. This kind of system is very common in large distribution centers that always ship orders in large variety.
When designing a pick module system here, the key factor to consider will be the layout of your facility. Alongside this, there are definite picking requirements that you have to determine. Consider the type of units that are being picked such as full pallets, carton, single items, etc. Find out the inventory being handled with its weight and the many different types of units that should be sorted and picked. Be sure you are informed of your lead time requirements. Consider your ceiling height and the entire square footage in your warehouse or storage facility.
A slotting analysis is typically done to determine the most cost-efficient place to store each of the different inventory items. During this process, you need to consider several factors. These comprise the weight and size of the product, the packaging including pallet, cartons, etc., labor and space costs, and the frequency and quantities that the item is being picked or replenish. View http://www.britannica.com/technology/warehouse to know more about warehouses.
Pick module systems entail permits that can be taken from the local city or state municipalities. This will make sure that the systems were assembles in such a way that building standards are stringently followed. These standards could vary from one place to another so it is suggested to have the designed reviewed prior to starting your project. There are three items that are primarily considered and these include structural analysis, fire safety and proper emergency lighting. You need to be more specific with fire safety standards so you have to give the most attention to its design. Normally, designing the systems entails CAD drawings and engineer calculations as a result of its complexity.
After the design is approved and essential permits are obtained from this website, you can start already the construction of your pick module systems. This will need some time based on the size and complexity of the system to be installed. It is advisable to create a design that will permit for future expansion. Though it could seem too early to consider the changes that need to occur to your design in the future, it helps to enable such changes so you will be ready by the time you need to expand.